High-performance material from nature: Fiber-reinforced semi-finished products made from hemp fibers
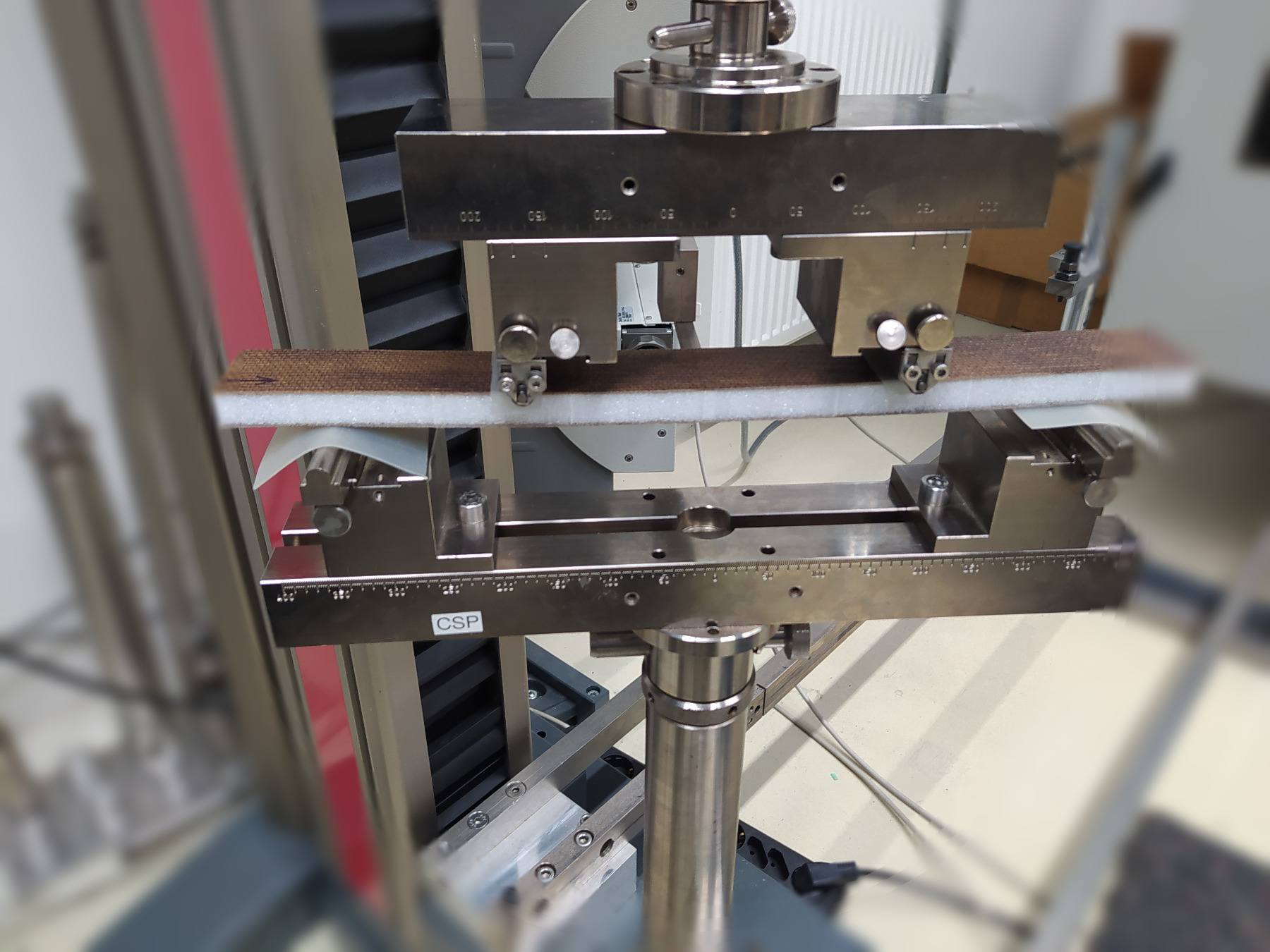
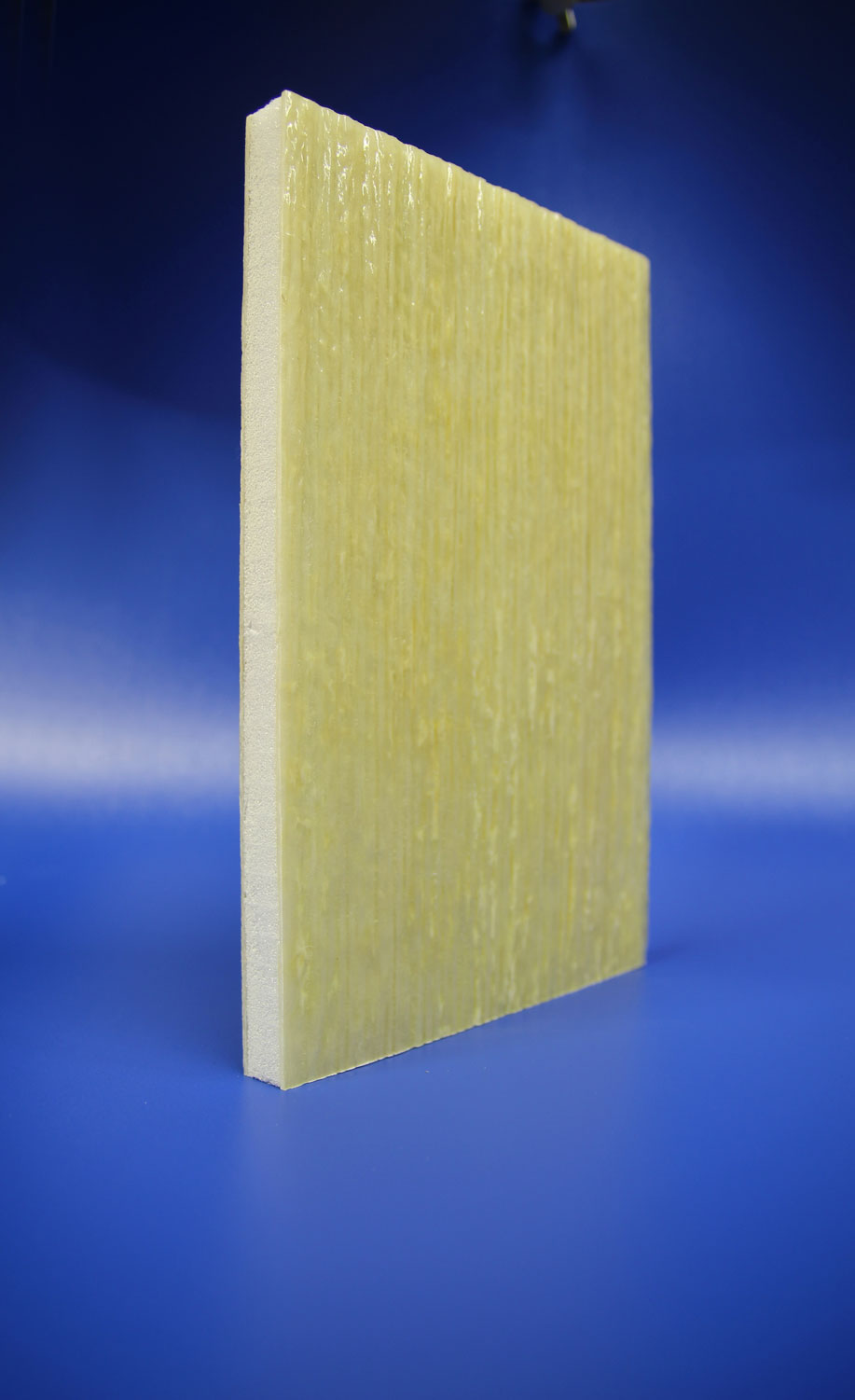

The use of renewable natural fiber composite plastics (NFRP) as semi-finished products for lightweight construction applications is currently being researched at the Fraunhofer Institute for Microstructure of Materials and Systems IMWS. The novel NFRPs are expected to drive the sustainable industrial use of bio-based composite plastics and can replace or complement conventional fiber composite plastics (FRPs).
The potential applications of fiber-reinforced composites (FRP) are growing steadily. They are preferably used as lightweight products in the aircraft and automotive industries and often consist of petroleum-based plastics and inorganic fibers (for example carbon or glass fibers). They are already making a contribution to environmental protection, as the lighter vehicles in which such materials are used consume less fuel.
Conventional FRPs are composed of inorganic reinforcing fibers and a polymer matrix. The matrix surrounds the fibers, which conduct the forces, and the combination of the properties of the fiber and matrix results in high stiffness as well as tensile strength of the fiber-matrix semi-finished product. As the awareness of energy balances of materials and the use of sustainable materials become more important, the demand for plastics made from renewable and biodegradable raw materials, so-called natural fiber-reinforced plastics, is also increasing. These consist of a plastic matrix that gets its strength from incorporated natural fibers, for example from hemp or flax.
Such semi-finished products become even more sustainable if the polymer matrix itself also consists of bio-based materials and native plant fibers are used for the embedded reinforcing fibers. NFRPs also have potential for lightweight construction applications in composites with thermoset matrix materials due to their low specific density. In addition, at the end of a component's life, they can be thermally recycled in existing recycling systems in an almost CO2-neutral manner. Hemp fiber in particular offers great potential here, both ecologically and technically, and could be the starting point for establishing local value chains.
This is the starting point for a project launched in September 2019 by the Fraunhofer IMWS and SKZ - KFE gGmbH, which specializes in the broad range of fiber composite plastics. The joint research project, which will run until February 2022, will investigate the use of sustainable NFRPs as an alternative solution to conventional fiber-reinforced plastics, with the raw materials used not competing with the food industry. The project partners aim to develop a pre-impregnated fiber semi-finished product, also known as prepreg, using hemp fibers and a resin matrix from renewable sources.
The prepreg technology enables uncomplicated handling as well as an optimal combination of fiber and matrix. These precursors can later be used to make a variety of high-quality components, such as car body parts. "Natural fiber composites have some weak points compared to conventional FRP. We have some good ideas on how to start right there and improve. Our goal is to produce prepregs that are not only particularly sustainable, but also efficient and reproducible to process" says project leader Sven Wüstenhagen, from the "design and manufacturing" group at the Fraunhofer IMWS.