Automated manufacturing processes for rotor blades made from recyclable thermoplastic composites that can be produced in large quantities are being developed by three Fraunhofer Institutes in the recently launched "Thermo-Blade-Spine" project. The Fraunhofer Institute for Microstructure of Materials and Systems IMWS is contributing its expertise in application-oriented UD tape development, the dimensioning and production of thermoplastic components and sustainability analyses.
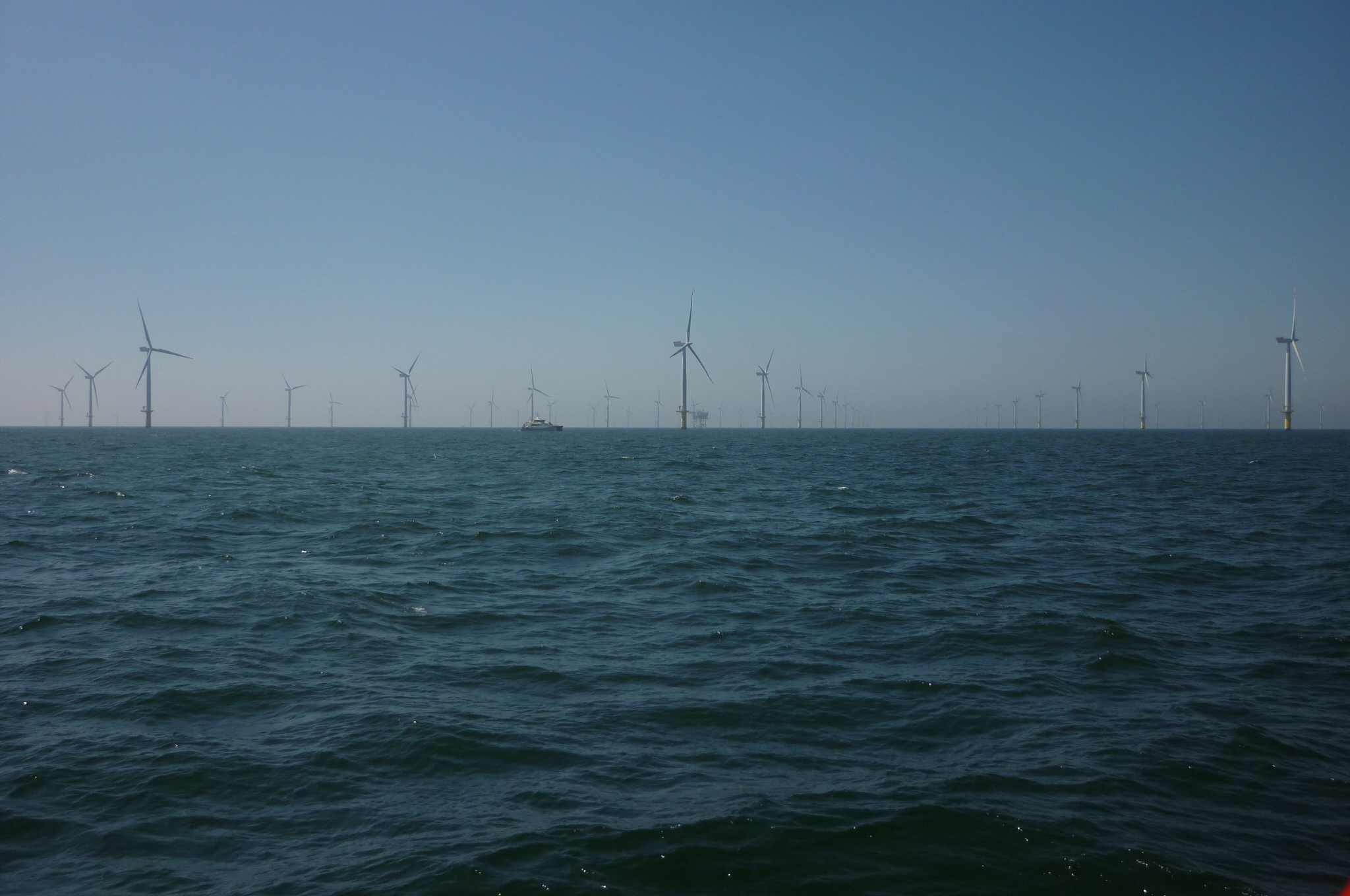
A lot of manual labor and non-recyclable composite materials are used in the production of rotor blades. This results in quality variations, production being relocated abroad due to cost pressure in the industry and a disposal problem. Circular, automated production can provide a remedy. However, initial approaches have not been successful due to high costs and difficult handling. In the "Thermo-Blade-Spine" project, which is funded by the Fraunhofer-Gesellschaft's internal "Prepare" program, the research teams involved are developing suitable technology solutions for automated manufacturing processes for the efficient production of rotor blades made from recyclable thermoplastic composites.
Wind turbine rotor blades are complex components and are critical to ensure efficient energy conversion and structural integrity. They are typically made from glass fiber reinforced plastics (GFRP) or carbon fiber reinforced plastics (CFRP) to ensure that they are aerodynamically shaped and can handle the enormous mechanical loads. Sometimes other materials such as balsa wood or foams are used for reinforcement. Rotor blades obtain their load-bearing capacity from a combination of longitudinal belts, which counteract bending, and stiffening spars or webs, which absorb additional tensile and compressive forces. The belts consist of many layers of unidirectional glass or carbon fibers, while the webs are manufactured in sandwich construction.
As rotor blades are getting bigger and bigger, the demands on their quality and reliability are increasing, which makes manual production even more difficult. Current onshore turbines typically have rotor blades with a length of 40 to 80 meters; for offshore turbines, this figure can rise to over 100 meters. Another challenge for manufacturers is disposal: The fiber-reinforced plastics (FRP) used in rotor blades since the 1980s consist of thermoset-based resins, which make it almost impossible to recycle the materials they contain. Currently, used rotor blades are either landfilled, shredded (the material is used as a sand substitute in the cement industry, for example) or incinerated.
A cycle-oriented, automated production of components with recyclable materials could solve both the problem of production and the lack of suitability for recycling if it works reliably and efficiently and allows competitive manufacturing costs. This is exactly what the participants in "Thermo-Blade-Spine" want to make innovative contributions to. They are aiming to develop and scale up automated high-rate manufacturing processes for rotor blades, using thermoplastic composites (TPC).
TPCs are characterized by excellent mechanical properties, can be processed and joined in automated processes and can be recycled due to their meltability. The CONTIjoin process developed at the Fraunhofer IWS is used to automatically construct the main belts using semi-finished tapes (UD tapes) pre-produced by the Fraunhofer IMWS. By using innovative thermoplastic composite and sandwich components and associated construction methods, automated and sustainable production can be realized and energy-intensive processes can be replaced. One of the results of the project, which will run until March 2027, will be an 18-metre-long rotor blade half-shell including belt and web segments manufactured at Fraunhofer IWES as a demonstrator.
As part of the project, the Fraunhofer IMWS is developing the thermoplastic, continuous fibre-reinforced semi-finished products for the belt in an efficient manufacturing process and transferring the optimized process to pilot scale by increasing the width of the semi-finished product tenfold. Furthermore, the load-compliant dimensioning and production of the thermoplastic belt web structures inside the rotor blade is carried out. Based on the development of suitable sandwich configurations, large-scale components are then developed and produced on an industrial scale.
In order to ensure the safe assembly of the large components, various joining concepts and pre-treatment technologies are considered and their properties are examined on a macroscopic and microscopic level. Based on these results, an 18-metre-long shear web is ultimately manufactured and joined to the previously produced half-shell.
In addition to the development points described above, the Fraunhofer IMWS is working with the partners on sustainability analyses and a holistic assessment of the CO2 equivalent reduction by comparing rotor blade production using the current state of the art and thermoplastic construction methods for the relevant materials and processes.
"Thermo-Blade-Spine" aims to prove that the production of rotor blades can also be carried out cost-effectively and sustainably in high-wage countries using automation. The project thus provides an important building block towards a zero-waste wind turbine. At the same time, the results make it possible to reduce Germany's dependence on international supply chains in a strategically important industry.