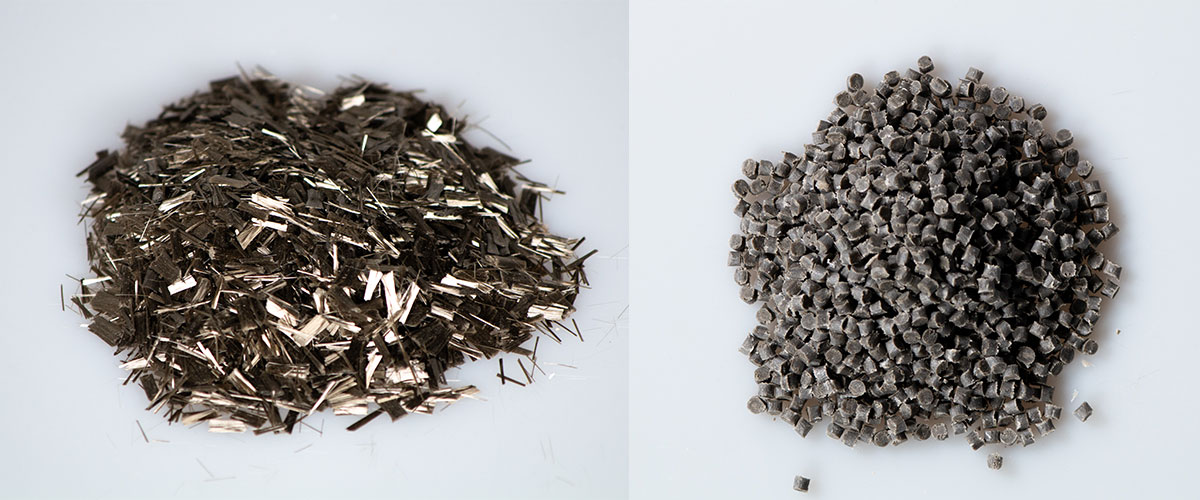
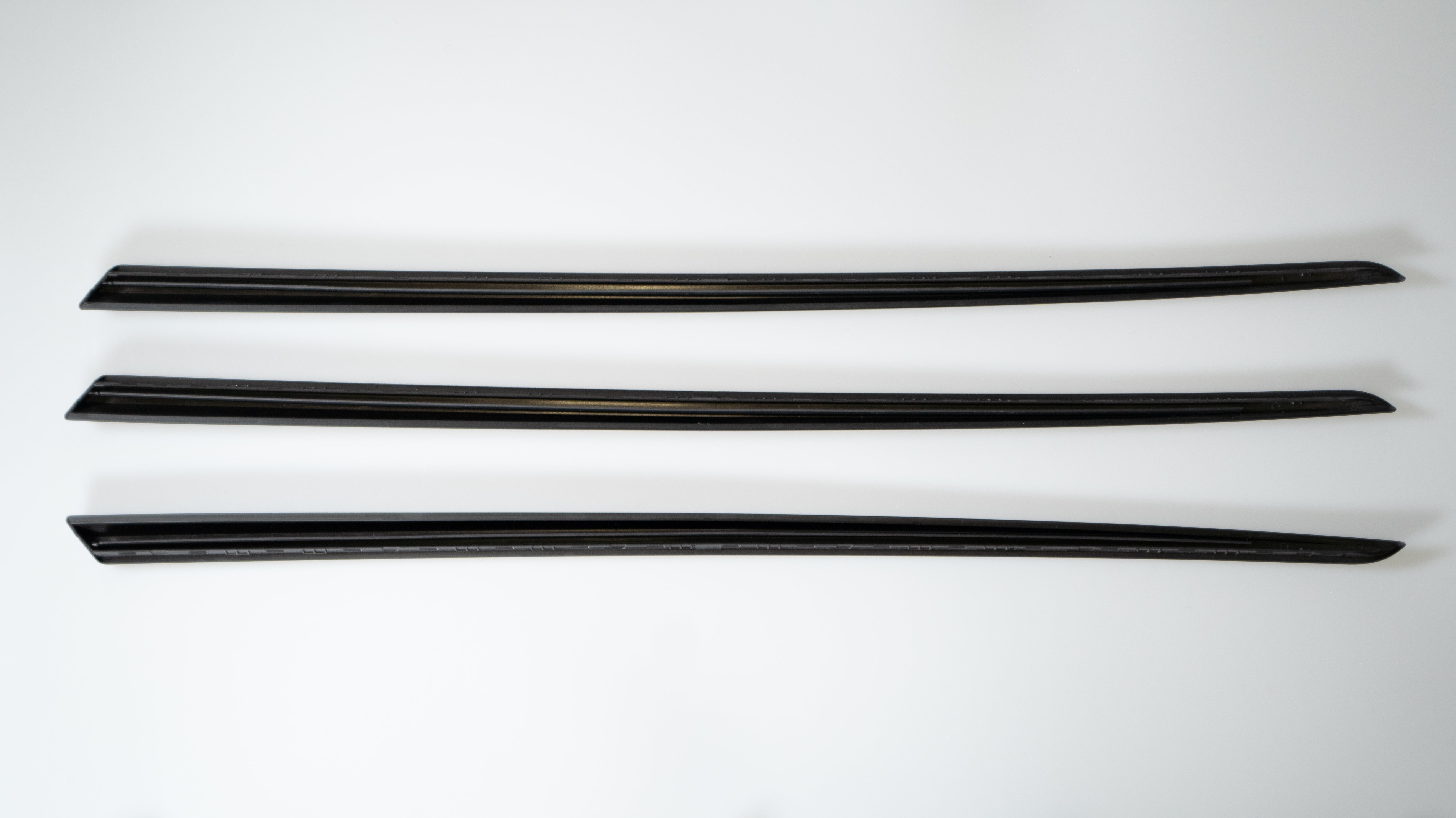
![BMBF_CMYK_Gef_M [Konvertiert]](/en/kompetenzfelder/kunststoffe/highlights/basalt-fiber-reinforced-polymer-compounds-lightweight-construction-applications-basaprop/jcr:content/contentPar/sectioncomponent/sectionParsys/textwithinlinedimage/imageComponent3/image.img.jpg/1721722213001/BMBF-gefoerdert-en-NEU.jpg)
Compared to glass fibers, basalt fibers offer considerable advantages in terms of energy consumption and environmental friendliness when used as a reinforcing component in thermoplastics. In the "BasaProp" project, the Fraunhofer Institute for Microstructure of Materials and Systems IMWS in Halle (Saale) and partners from industry have optimized the pre-treatment and packaging of basalt chopped fibres so that they can be processed better and provide optimal compound properties. An automotive strip produced by injection molding as a project result demonstrates the potential of this material combination.
Glass fiber reinforced plastics play an important role in the automotive industry (e.g. for body parts, bumpers, hoods), aerospace (aircraft fuselage parts, wings, rotor blades) or for sports equipment (tennis rackets, bicycles, skis). They offer high strength, rigidity and corrosion resistance. However, the production of glass fibers is energy-intensive and therefore costly. With respect to this, compounds with basalt fibers as a reinforcing component can score points. These fibers made from basaltic lava rock are also more environmentally friendly to use.
Basalt fibers have an around five percent higher density than E-glass fibers, but they exceed their tensile strength and stiffness values by up to 15 percent, and they offer high thermal and chemical resistance. Due to their lower surface functionalities, however, they have so far been difficult to incorporate into a matrix of polyolefins because they do not adhere sufficiently well. Fiber reinforced thermoplastics are frequently used in the packaging industry or in the construction industry, for example, where basalt fibers are not yet able to fully exploit their potential in thermoplastic compounds.
In order to improve the composite properties, Deutsche Basalt Fiber GmbH (DBF), Polyram MCT Germany GmbH, SLM Kunststofftechnik GmbH and the Fraunhofer IMWS have bundled their expertise in the "BasaProp" project. "We have optimized the dimensions of basalt fibers so that they adhere significantly better to the matrix and have thus proven that they are suitable for innovative injection molding applications," says Patrick Hirsch, Group Manager "Sustainable Materials and Processes" at the Fraunhofer IMWS.
As a demonstrator, the project partners have produced an injection-molded strip for the exterior of cars from basalt fiber-reinforced polypropylene. The Fraunhofer IMWS accompanied the material development with extensive material technology tests on a laboratory and pilot scale. In order to systematically determine the best possible dimensioning of the basalt fibers, a special methodology was developed to evaluate the fiber-matrix interaction in fiber-reinforced compounds. The research team was able to prove that a dynamic mechanical analysis provides relevant parameters for the evaluation of fiber-matrix adhesion. The storage modulus provides information on how a material reacts to mechanical loads and how it behaves under different temperature and frequency conditions.
Using the method developed in the project, it was possible to quantitatively evaluate various parameters based on mini-samples produced on laboratory-scale compounding systems. In this way, optimal sizes for different matrix polymers could be determined. A sizing process was then developed that allowed the production of chopped basalt fibers in a quantity sufficient for upscaling the compounding process.
"The mechanical properties were significantly better than previous solutions with basalt fiber-reinforced polypropylene composites. We were also able to make significant progress in terms of suitable compound formulations and efficient compounding technologies. This opens up new fields of application for these fibers, especially as a replacement for conventional glass fiber composites," says Hirsch.