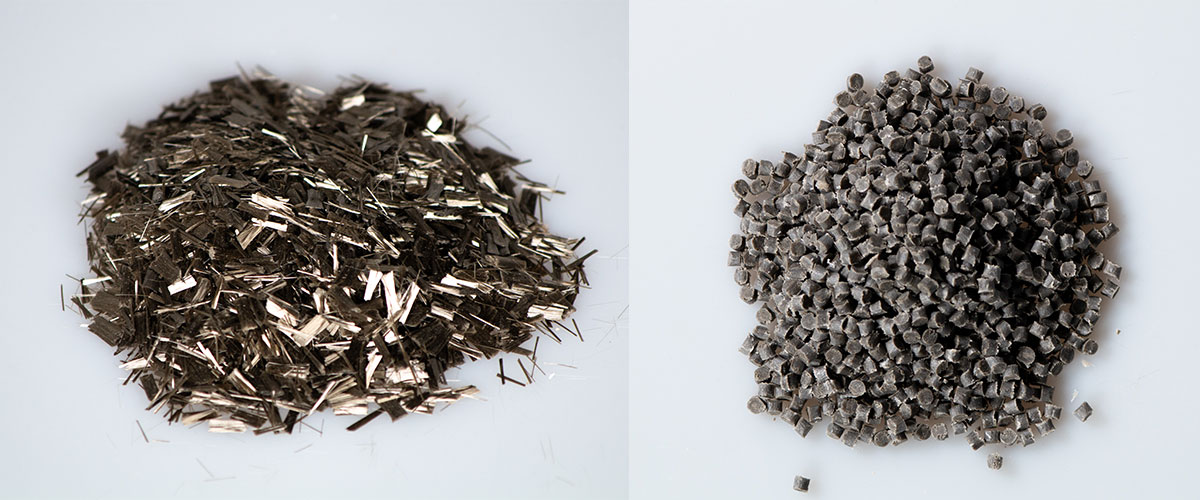
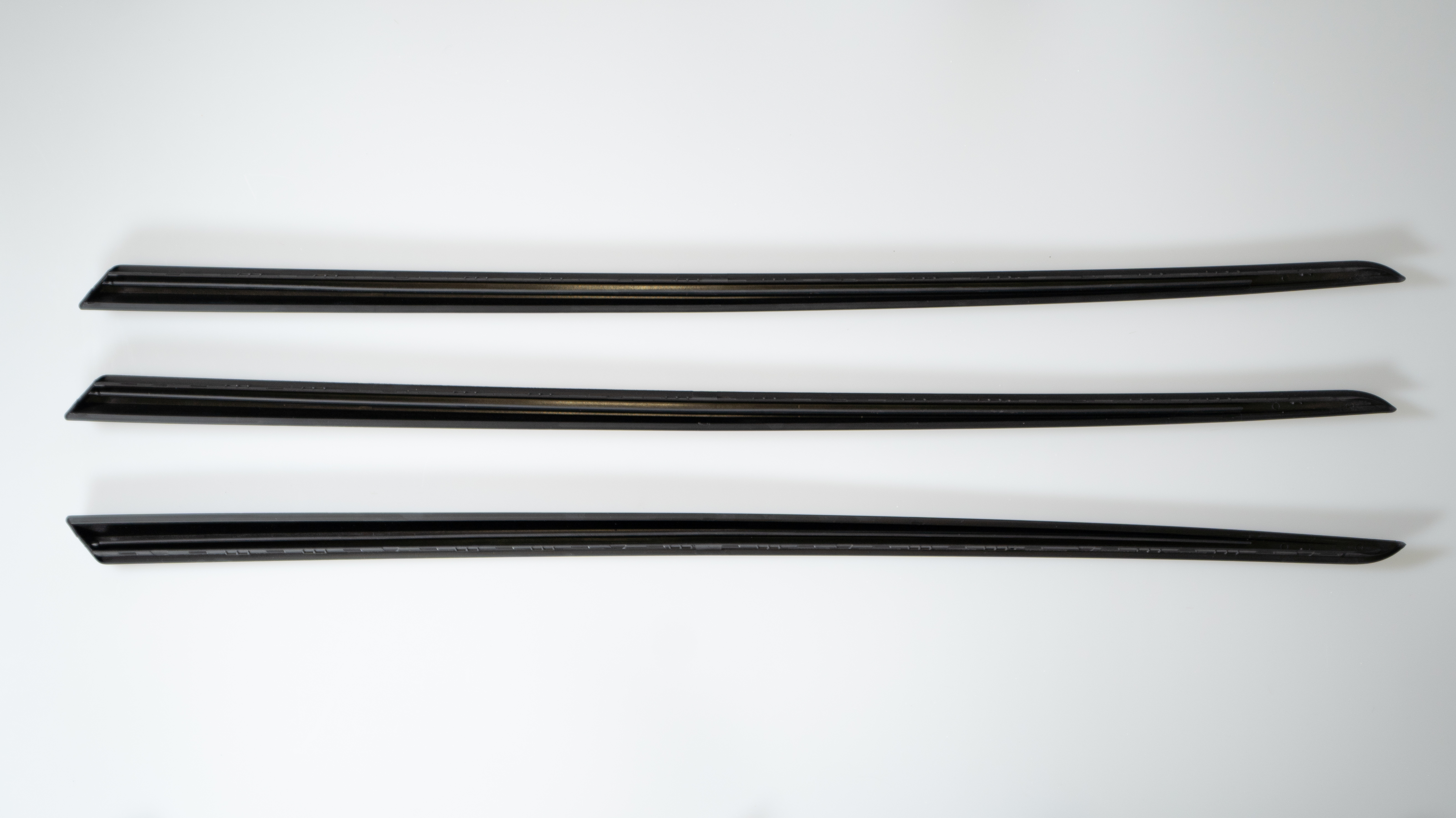
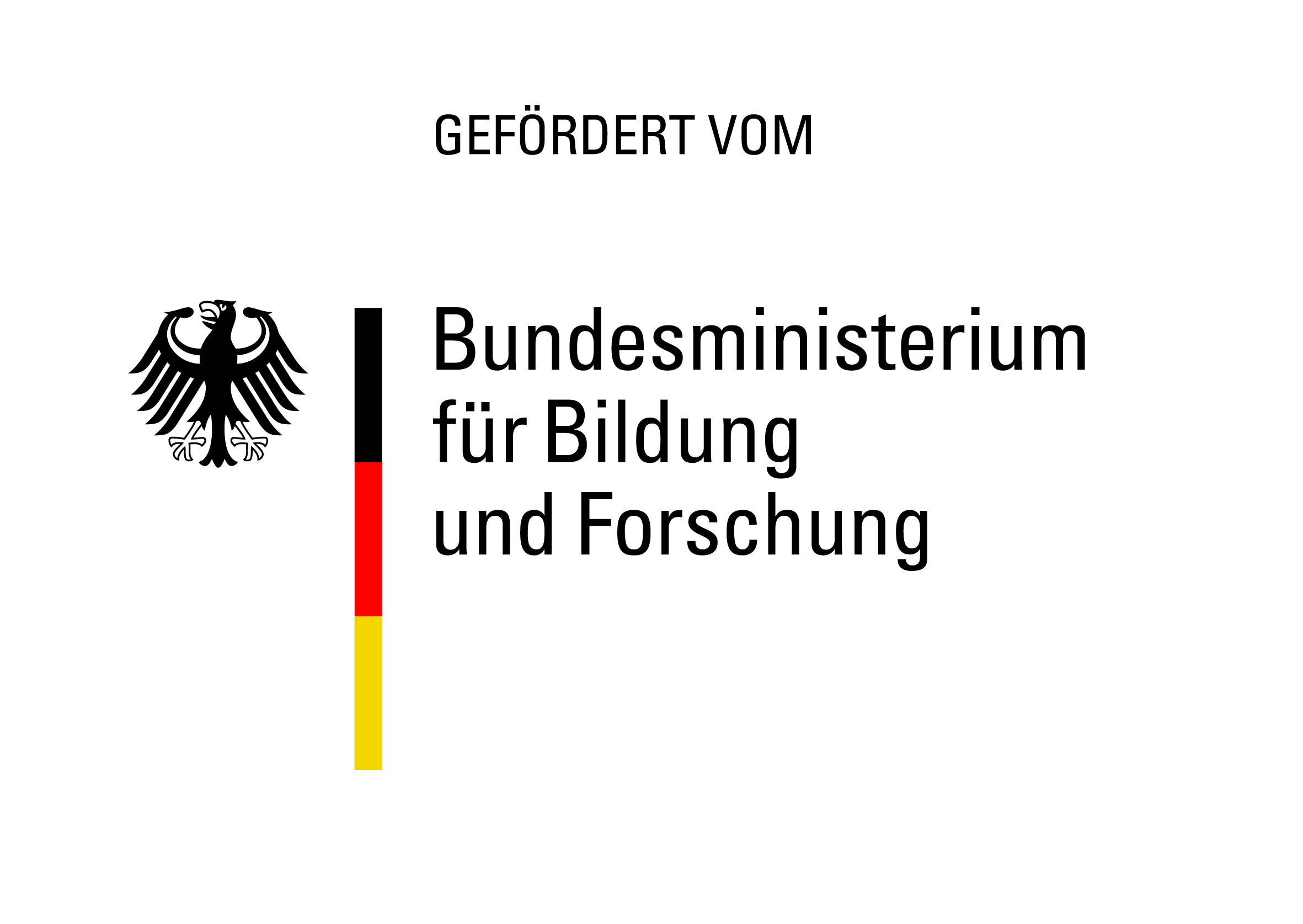
Im Vergleich zu Glasfasern bieten Basaltfasern erhebliche Vorteile bei Energieverbrauch und Umweltfreundlichkeit, wenn sie als Verstärkungskomponente in thermoplastischen Kunststoffen eingesetzt werden. Im Projekt »BasaProp« haben das Fraunhofer-Institut für Mikrostruktur von Werkstoffen und Systemen IMWS in Halle (Saale) und Partner aus der Industrie die Vorbehandlung und Konfektionierung von Basalt-Schnittfasern optimiert, sodass sie sich besser verarbeiten lassen und optimale Compound-Eigenschaften erbringen. Eine im Spritzguss hergestellte Automobil-Leiste als Projektergebnis demonstriert die Potenziale dieser Materialkombination.
Glasfaserverstärkte Kunststoffe spielen eine wichtige Rolle in der Automobilindustrie (etwa für Karosserieteile, Stoßstangen, Motorhauben), Luft- und Raumfahrt (Flugzeugrumpfteile, Tragflächen, Rotorblätter) oder für Sportgeräte (Tennisschläger, Fahrräder, Ski). Sie bieten eine hohe Festigkeit, Steifigkeit und Korrosionsbeständigkeit. Die Herstellung von Glasfasern ist allerdings energie- und damit kostenintensiv. Hier können Verbundwerkstoffe mit Basaltfasern als Verstärkungskomponente punkten. Diese Fasern aus basaltischem Lavagestein sind zudem umweltfreundlicher im Einsatz.
Basaltfasern haben eine etwa fünf Prozent höhere Dichte als E-Glasfasern, dafür übertreffen sie deren Werte bei Zugfestigkeit und Steifigkeit um bis zu 15 Prozent und bieten zudem eine hohe thermische und chemische Beständigkeit. Aufgrund ihrer geringeren Oberflächenfunktionalitäten lassen sie sich bisher allerdings nur schwierig in eine Matrix aus Polyolefinen einbringen, weil sie dort nicht ausreichend gut haften. Diese Gruppe von Kunststoffen wird beispielsweise in der Verpackungsindustrie oder im Bauwesen häufig genutzt – überall dort können Basaltfasern ihr Potenzial in thermoplastischen Verbindungen also noch nicht vollständig zur Geltung bringen.
Um die Verbundeigenschaften zu verbessern, haben die Deutsche Basalt Fiber GmbH (DBF), die Polyram MCT Germany GmbH, die SLM Kunststofftechnik GmbH und das Fraunhofer IMWS im Projekt »BasaProp« ihre Kompetenzen gebündelt. »Wir haben die Dimensionen von Basaltfasern so optimiert, dass sie deutlich besser in der Matrix haften und somit den Nachweis erbracht, dass sie für innovative Spritzguss-Anwendungen geeignet sind«, sagt Patrick Hirsch, Gruppenleiter »Nachhaltige Werkstoffe und Prozesse« am Fraunhofer IMWS.
Die Projektpartner haben als Demonstrator eine spritzgegossene Leiste für den Außenbereich von Autos aus einem basaltfaserverstärkten Polypropylen gefertigt. Das Fraunhofer IMWS begleitete die Materialentwicklung mit umfangreichen materialtechnischen Untersuchungen im Labor- und Pilotmaßstab. Um systematisch die optimale Dimensionierung der Basaltfasern zu ermitteln, wurde eine spezielle Methodik zur Bewertung der Faser-Matrix-Wechselwirkung in faserverstärkten Verbindungen entwickelt. Das Forschungsteam konnte nachweisen, dass eine dynamisch mechanische Analyse relevante Parameter für die Bewertung der Faser-Matrix-Haftung liefert. Der Speichermodul gibt Aufschluss darüber, wie ein Material auf mechanische Belastungen reagiert und wie es sich unter verschiedenen Temperatur- und Frequenzbedingungen verhält.
Mit der im Projekt entwickelten Methode war eine quantitative Bewertung verschiedener Größen auf der Grundlage von Mini-Proben möglich, die auf Compoundieranlagen im Labormaßstab gefertigt wurden. Auf diese Weise konnten optimale Größen für verschiedene Matrixpolymere ermittelt werden. Daraufhin wurde ein Schlichteverfahren entwickelt, das die Herstellung von zerkleinerten Basaltfasern in einer Menge erlaubte, die für ein Upscaling des Compoundierprozesses ausreicht.
»Die mechanischen Eigenschaften waren deutlich besser als bei bisherigen Lösungen mit basaltfaserverstärkten Polypropylen-Verbundwerkstoffen. Wir konnten zudem entscheidende Fortschritte für geeignete Compound-Rezepturen und effiziente Compoundier-Technologien erzielen. Das eröffnet neue Anwendungsfelder für diese Fasern, insbesondere als Ersatz für herkömmliche Glasfaserverbundwerkstoffe«, sagt Hirsch.