Five partners from Central Germany want to jointly develop bio-based, continuous fiber-reinforced UD tapes for lightweight construction and at the same time create solutions for production up to pilot scale. The Fraunhofer Institute for Microstructure of Materials and Systems MWS, the Fraunhofer Institute for Applied Polymer Research IAP, Merseburg University of Applied Sciences, DOMO Engineering Plastics GmbH and DBF GmbH are working together to achieve this. They are relying on a combination of bio-based polyamide as a matrix and basalt fibers as a reinforcing component.
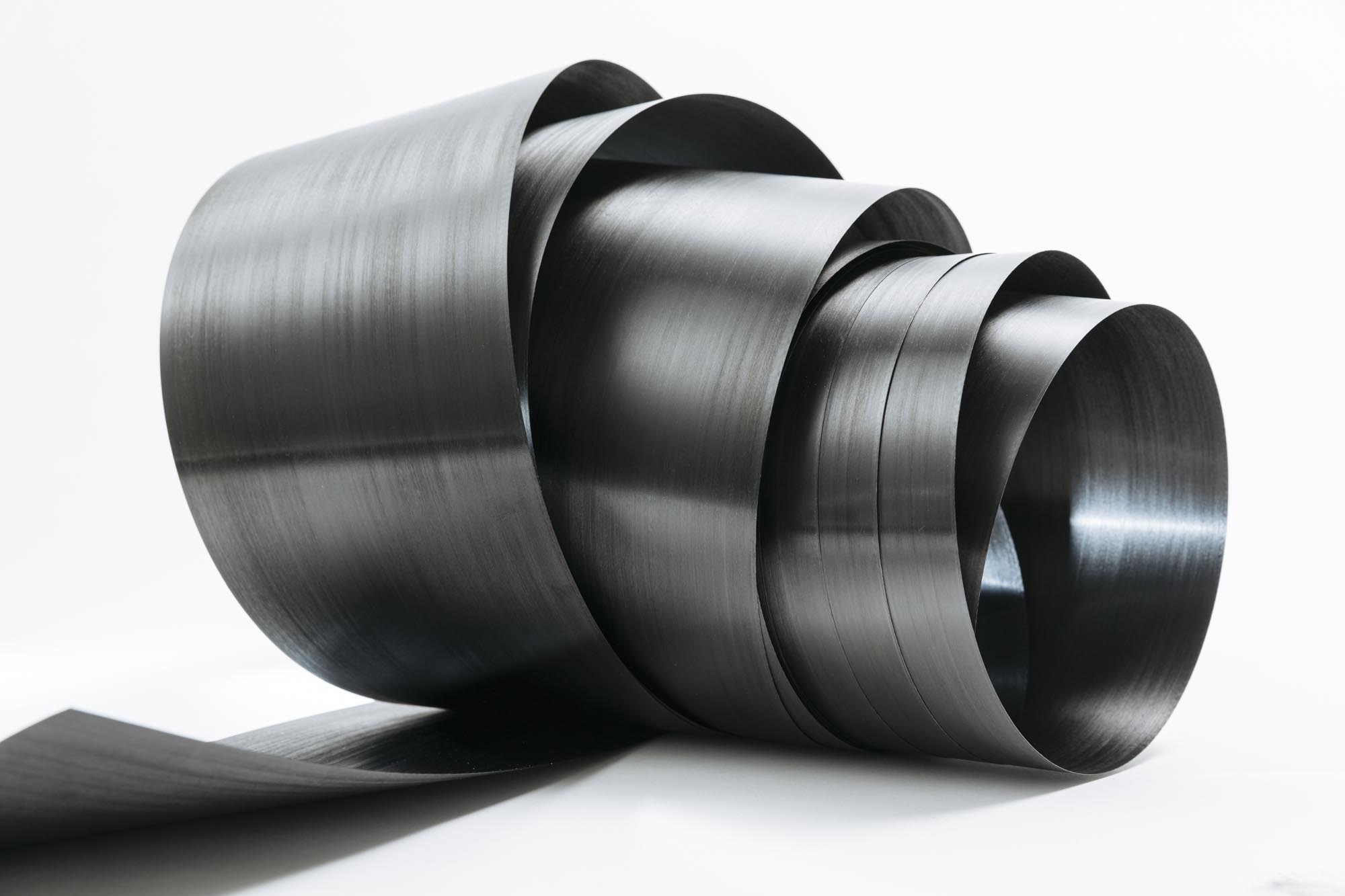
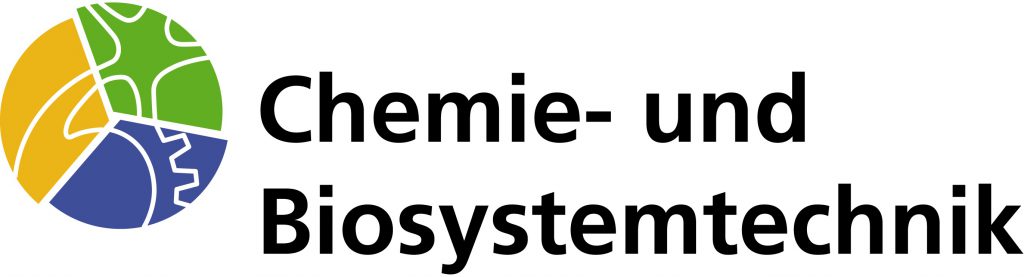
Continuous fiber-reinforced semi-finished products (UD tapes) are increasingly in demand for applications with high mechanical component requirements. Their advantage: they enable high strength and rigidity, high fatigue strength, high corrosion resistance and good resistance to chemicals - all at a very low weight. This effect is achieved because the continuous reinforcing fibers in the tapes are arranged in a single direction. The fibers are impregnated with a matrix of resin or thermoplastic polymers and formed into a very thin band with a high fiber content (tape). The targeted superposition of several tapes, which is possible in a wide variety of directions, allows the mechanical properties of a component to be optimized locally and in line with specific requirements, particularly in structural applications.
In addition to thermoset-based systems (so-called prepregs), thermoplastic-based UD tapes are also increasingly in demand in sectors such as the automotive industry, aviation, container construction and the sports industry. Compared to thermosets, they offer many advantages such as recyclability and efficient processing methods. If these continuous fibre-reinforced semi-finished products can be produced as bio-based materials, their added value will increase even further.
"Given the industry's interest in sustainable solutions, bio-based, thermoplastic UD tapes are the next logical step in value creation. In our project, we therefore want to pave the way for such tapes with the highest possible bio-based content and attractive mechanical properties," says Ivonne Jahn, who heads the project "Bio-based polyamide tapes for lightweight structural construction (Bio-PA tape)" at the Fraunhofer IMWS.
The project, which is funded by the High Performance Center for Chemical and Biosystems Engineering, aims to develop bio-based polyamide (PA) matrices with optimized material and processing properties. Sustainable basalt and regenerated cellulose fibers are being tested as reinforcing fibers. The project objectives also include proving that the materials and processing methods developed are suitable for the production of sample quantities on a pilot scale. The development work is therefore being carried out at the Fraunhofer Pilot Plant Center for Polymer Synthesis and Processing PAZ in Schkopau, where the corresponding facilities are operated.
At the Fraunhofer IAP, suitable bio-PA types are initially to be developed on a laboratory scale for use in UD tapes. Of particular relevance here are good flow properties for optimal wetting of the fibers in the UD tape process. In a second step, the synthesis process will be transferred to pilot scale. The Fraunhofer IMWS develops the tape and the process technology for its production from these manufactured materials. The focus here is on the melt impregnation process for various bio-PA tapes of different formulations, also on a pilot scale. The semi-finished products are then characterized in terms of material technology at Merseburg University of Applied Sciences. The partners Domo and DBF provide raw materials (bio-PA and basalt fibers) for the tape development as well as reference materials.
"We want to pave the way for new material solutions as well as show local industrial partners attractive ways of utilizing their materials through proof of concepts. In addition to the demonstrator materials produced, the result should also be significantly advanced manufacturing processes. We are aiming for a level of maturity that can be directly transferred to industrial processes," says Jahn.