Standardized test procedure for quality controls on sandwich components subject to high loads
Sandwich structures enabling lightweight construction, such as those used in the aircraft industry, in rotor blades at wind power plants or lightweight vehi-cles, consist of fixed top layers which are separated by an extremely light-weight core material. Mechanically they are very resilient and at the same time extremely light. However, if the rigid connection between the top layer and the core is damaged by improper loading, in extreme cases this can lead to the failure of the component. The Fraunhofer Institute for the Microstructure of Materials and Systems IMWS has developed a standardized test procedure based on its findings about the microstructure of such components using in-situ X-ray tomography to examine fracture toughness, so as to reliably predict the load limits of such sandwich structures and prevent damage.
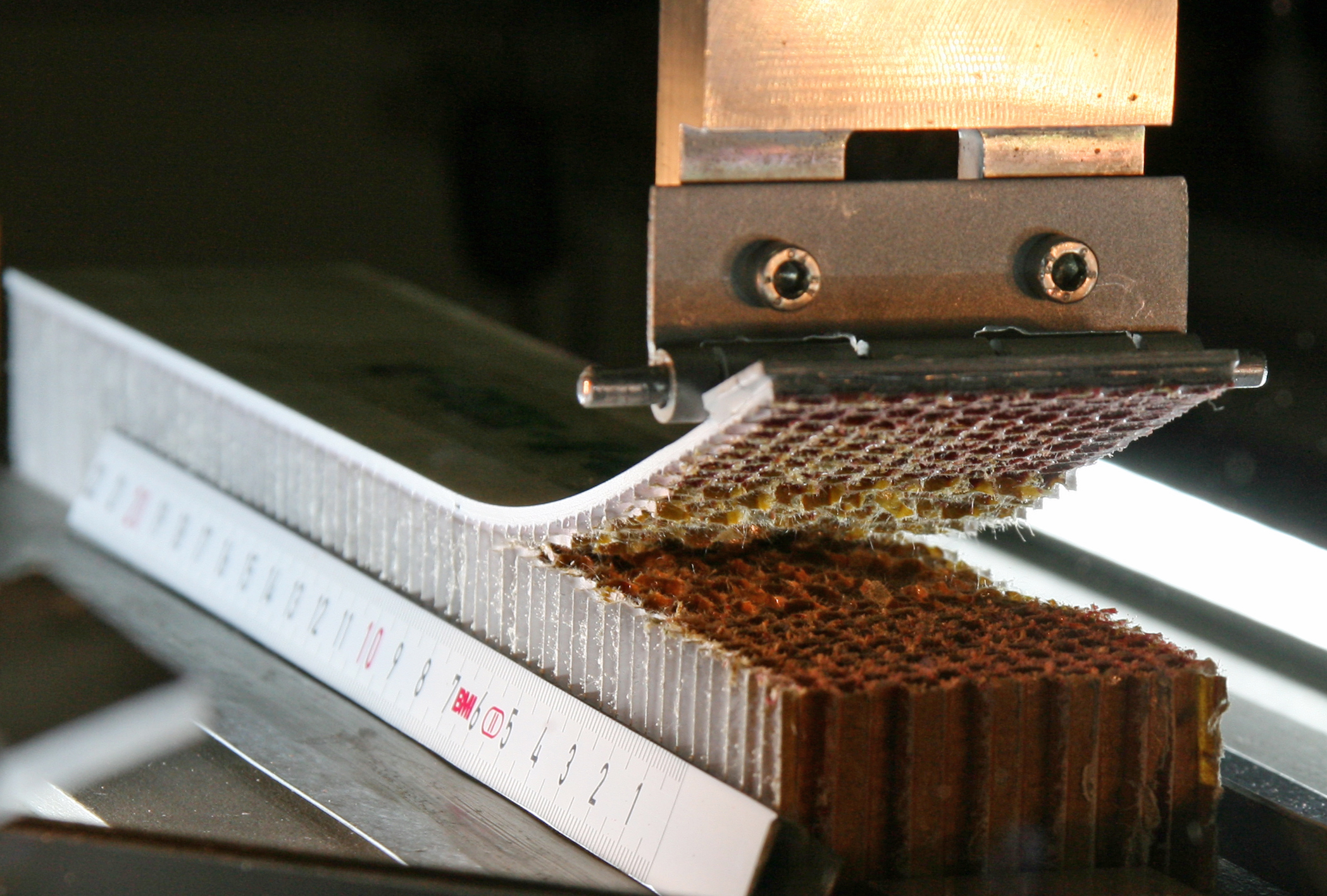
Structural components subject to high mechanical stress for the automobile industry or aircraft and space vehicles are often manufactured using the sandwich construction technique. Load-bearing top layers are joined with a lightweight sandwich core and separated from the latter. Using extremely thin top layers made of fiber-reinforced plastic (FRP) and a very lightweight and stable core material with a honeycomb structure, it is possible to attain high degrees of mechanical stability with a minimum weight. Such sandwich structures can lead to considerable weight savings. This in turn lowers fuel consumption and is environmentally friendly.
The load-bearing top layer may separate from the supporting core following impact stresses, overloading or as a result of errors during manufacturing or repair work; this is known as “disbond" damage. If the damage initially remains undiscovered due to the limited extent of the damage or because it is not directly visible, it may continue to spread during continued use of the component, reduce the load-bearing capacity of the sandwich structure and in some cases lead to the complete loss of the component’s integrity.
In a research project promoted by the Federal Ministry for Economic Affairs and Energy and conducted together with the Institute of Aerospace Engineering TU Dresden, the Fraunhofer IMWS developed a standard test method enabling fracture toughness, as a way of quantifying the resistance of sandwich materials against the spreading of disbond damage – i.e. the local separation of the top layer from the core – to be analyzed and hence reliably predicted. “Our project centered on the specific characteristics of ultralight sandwich structures subject to high loads with honeycomb cores and extremely thin fiber composite plastic top layers”, says Dr. Ralf Schäuble, the project’s manager at the Fraunhofer IMWS.
Sandwich samples with artificially induced disbond damage were tested in what is referred to as a single cantilever beam test (SCB). A separated section of the top layer was continuously detached from the core using a loaded beam, forcing the crack to spread along the bond zone between the core and the top layer. The procedure is essentially comparable to the more familiar double cantilever beam test (DCB) for fiber composite laminates. An important constraint in this test procedure has previously been the requirement of linearity between force and displacement path during the test. However, such linearity is absent in the materials used in the research project. This led to the study of two alternative approaches for solving the problem and their assessment based on their feasibility and their suitability in fracture-mechanical terms.
“One option was the artificial stiffening of the top layer by attaching an elastically deformable plate with the aim of increasing its flexural rigidity such that the deformation during the testing was minimal enabling a higher degree of linearity to be obtained”, explains Schäuble. In this case, the evaluation of the test data (data reduction) can be performed on the basis of the relationships in linear beam theory (MBT, Modified Beam Theory) – based on the familiar procedure used in the standardized DCB test.
The other option consisted of testing the natural properties of the sandwich sample and making allowance for any significant non-linearity during data reduction by means of constructive measures in the test apparatus and the application of an alternative fracture-mechanical concept. Both variants were analyzed with regard to their materials-mechanical and fracture-mechanical aspects and experimentally validated. A decisive step forward was achieved in the understanding of the processes at work in the material through the use of in-situ X-ray tomography. By means of the high-resolution and contactless observation of the damage process inside the sandwich material under stress during the spread of the disbond damage, the existence of important connections between the microstructure of the sandwich composite material and the damage behavior was established and then suitably translated into simpler analytical calculation formulae – an important prerequisite for the practical applicability of the test procedure.
Based on the results a specification for carrying out the test procedure on lightweight honeycomb sandwich materials with very thin top layers was drawn up and incorporated into an international initiative for the standardization of the test.
“The test method developed by us is very promising”, says Schäuble commenting on the method developed. The data and results collected will flow directly into a new standard at the international standards organization ASTM and will be included in the CMH-17 Composite Materials Handbook – a handbook made up of several volumes recognized by international certification bodies and aviation regulatory bodies and used to interpret composite structures.