Efficient sandwich lightweight structures with high surface quality
Fiber composite plastics and sandwich construction are established lightweight construction technologies. They enable enormous savings in terms of weight when implementing highly loadable structural components and are used for aircraft and vehicle applications, for example. So far, what these components have been lacking for a wide range of applications are smooth, visually appealing surfaces. In a joint project, the companies ElringKlinger AG, Daimler Truck AG, ThermHex Waben GmbH, Edevis GmbH and the Fraunhofer Institute for Microstructure of Materials and Systems IMWS are working together to develop solutions and at the same time the appropriate processes for production and quality testing. The partners rely on metal-plastic hybrid sandwich materials.

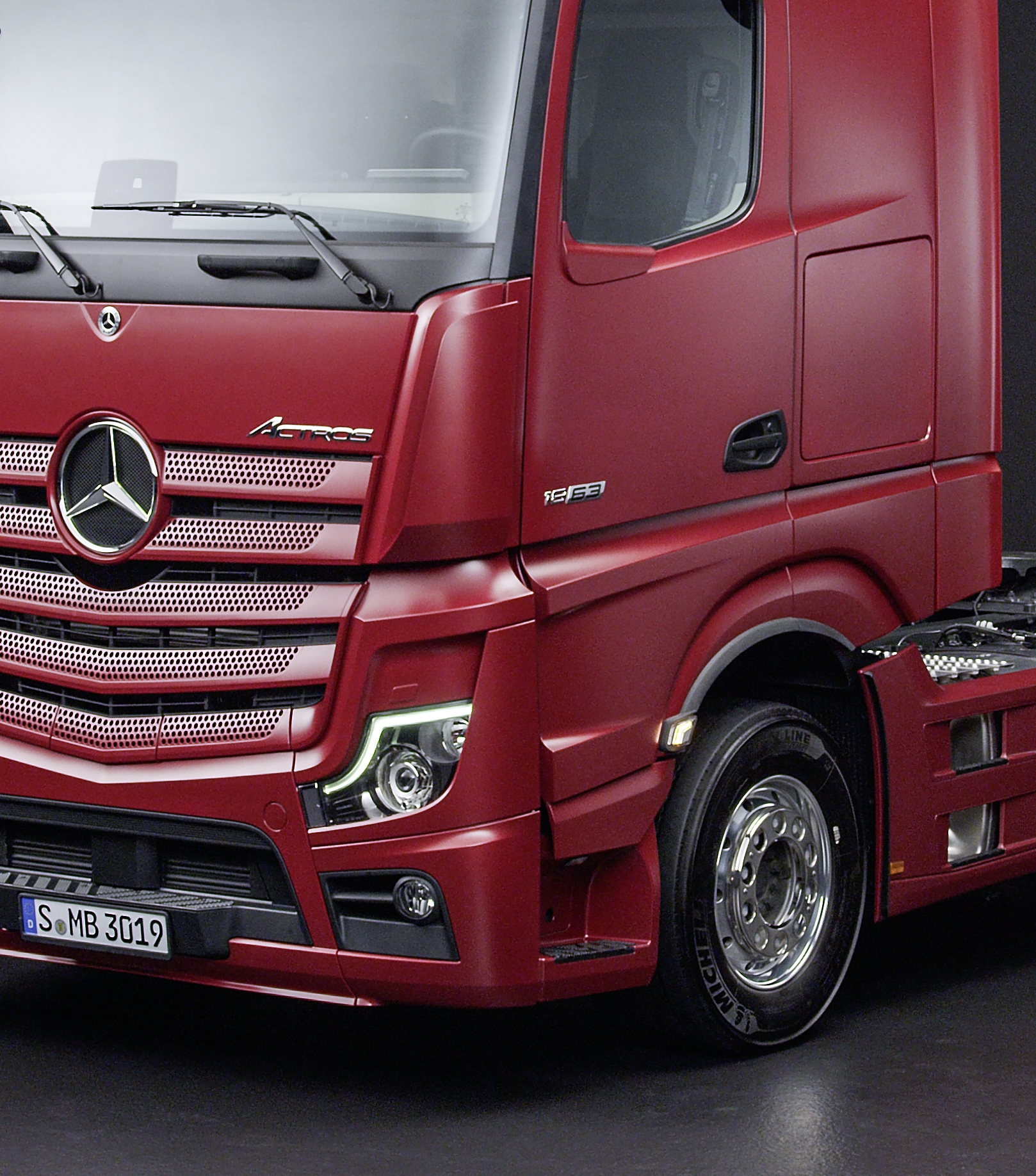
Particularly efficient lightweight construction solutions are achieved by the sandwich construction method, in which, for example, a light honeycomb-shaped support core is combined with thin and very stiff cover layers, resulting in high flexural rigidity combined with low density. In comparison with monolithic construction, this enables weight savings of up to 80 percent. Production solutions that are suitable for large-scale series production are available for the use of thermoplastic fiber-reinforced plastics in sandwich composites. In addition, these semi-finished products are easy to recycle. They are already being put to successful use for truck and caravan bodies.
A typical disadvantage of sandwich lightweight structures must be eliminated in order to open up further application possibilities: They do not feature a perfect surface, as is required in the automotive industry, for instance. Without extensive reworking, the reinforcing fibers are always visible on the surfaces; and the cover layers can sink into the honeycomb cells where the gaps of the support core are. The project partners intend to solve this problem by using honeycomb cores with particularly small cell widths and providing the fiber-reinforced components with a metallic top layer forming a smooth and thus optimal surface (Class A surface).
“We use organosandwich semi-finished products, i.e. a thermoplastic honeycomb core with reinforced cover layers of fiber composite plastic. These are additionally provided with metal cover layers, such as thin metal sheet or metal foil, which are bonded to the material. By using this metal-plastic hybrid material, we aim to exploit the enormous weight and cost-saving potential of sandwich construction and technology for the large-scale production of lightweight structures with demanding surface requirements,” says Matthias Biegerl, coordinator of the joint project at ElringKlinger.
As a means of demonstrating the efficiency of this approach, the project partners in the project, which is scheduled to run until October 31, 2022, intend to produce a demonstrator that corresponds to an existing component from a truck that is currently being manufactured using monolithic plastic injection molding technology: the lid of a storage compartment. The combination of the project partners’ expertise enables them to look not only at this component but also at the processing technology, functional integration and the testing process during manufacture. “Alongside the demonstrator, we want to develop design, process and quality assurance methods for metal-plastic hybrid sandwich materials on a pilot scale,” says Dr. Ralf Schlimper, project manager at the Fraunhofer IMWS.
The objectives of the research team therefore also encompass the development of suitable forming processes (including 3D-formed surfaces, thickness jumps, edge closure), functionalization using injection molding (including load introduction and functional elements) and the development of solutions for a non-destructive, inline-capable testing method based on active thermography. Active thermography is not only essential for quality assurance for future users, but also for coping with the material and process challenges during the research project. These challenges are the secure connection between the thermoplastic sandwich and the metallic top layer, the inspection of the surface quality as well as the control of the forming process, e.g. for the necessary thermal condition of the sandwich structure, which allows 3D molding without the core melting and thus becoming unstable.
Naturally, the project partners are also focusing on geometry/shaping, mechanical performance and reparability. For the creative diversity that results from the use of 3D-moldable sandwich composites, calculation methods for process and structural design as well as design recommendations for functionalization and component design are to be developed.
Biegerl summarizes the intended advantages: “We are focusing on making sandwich lightweight structures with Class A surface quality possible for the first time, while achieving a high degree of functional integration through cost-efficient gating of functional elements and inline-capable testing technology in a forming technology suitable for series production. The benefits of the sandwich idea, such as mechanical performance, weight savings and high cost-effectiveness of semi-finished product manufacture and component processing, are retained. We are therefore now able to pave the way for a broad market entry of this technology, especially in the automotive industry.”