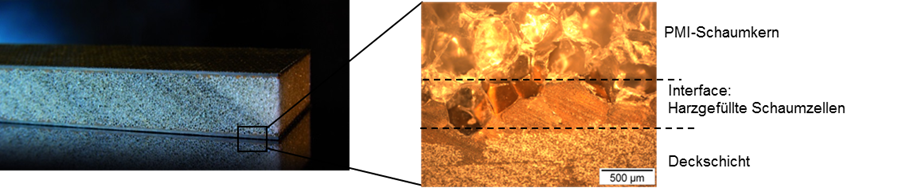
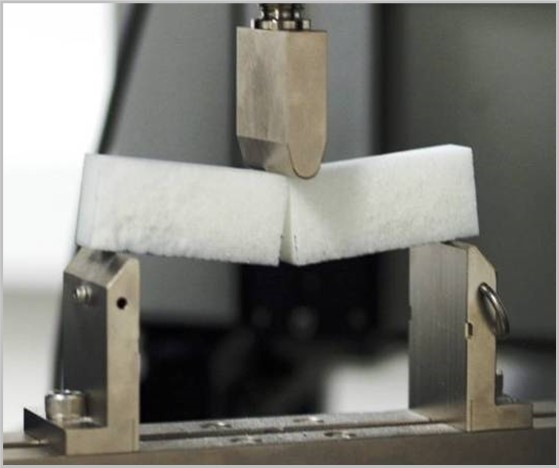
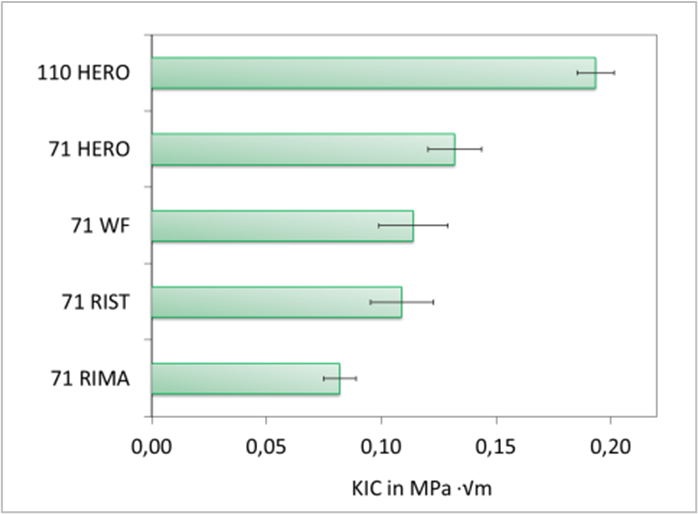
The sandwich construction with a rigid polymer foam core and carbon fibre-reinforced plastic cover layers offers high bending stiffness at low weight. However, the thin cover layers are susceptible to damage from low impact energies such as hail or falling tools. The SANDWICH² project within the aeronautics research programme LuFo V focuses on investigating and optimising the damage tolerance of such foam sandwich structures, in particular through a microstructure and mechanism-based assessment method. The Fraunhofer Institute for Microstructure of Materials and Systems IMWS is part of the research consortium and responsible for this research.
Evaluation methods for demonstrating the damage tolerance of foam sandwich structures
In the context of damage tolerance design for foam sandwich structures, a reliable assessment method is required to predict the propagation of local damage under service loads. Here, an interface crack between the differently stiff materials CFRP laminate in the top layer and rigid polymer foam in the core is considered (see Figure 1). Fracture mechanics parameters are experimentally evaluated to determine crack fracture toughness and crack propagation parameters. Special attention is paid to characterising the material mechanical behaviour of the foam core, as it is the weakest component and exhibits residual stresses due to manufacturing. A finite element analysis enables the prediction of the residual load-bearing capacity and residual service life, taking into account defined cover layer delamination. Validation is carried out using tests on structures close to the component.
Fracture mechanics characterisation of the foam core
To characterise the fracture mechanics of the closed-cell PMI rigid foam ROHACELL®, appropriate tests were first carried out on coupon specimens. Among other things, the 3-point bending test with a single edge notched bend (SENB) specimen was used to determine the fracture toughness KIC under Mode I load for foams of different cell size and density. It was found that the fracture toughness for foams with approximately the same density of, for example, 75 kg/m³ increases with increasing cell size (from 71RIMA with approx. 50 µm to 71WF with approx. 600 µm mean cell diameter, see Figure 3). In contrast, the PMI rigid foam HERO with toughness-optimised basic formulation shows increased fracture toughness characteristics despite comparatively small cell sizes (see Figure 2). For foams with a higher density, the determined fracture toughness values also generally increase significantly (from 71HERO with 75 kg/m³ to 110HERO with 110 kg/m³).