Researchers at the Fraunhofer Institute for Microstructure of Materials and Systems IMWS have developed a new method that allows microstructures to be incorporated into plastics using infrared lasers. Laser swelling opens up a very wide range of potential applications, from new treatment options for short-sightedness to VR glasses, compact microscopes and optics for LED displays.
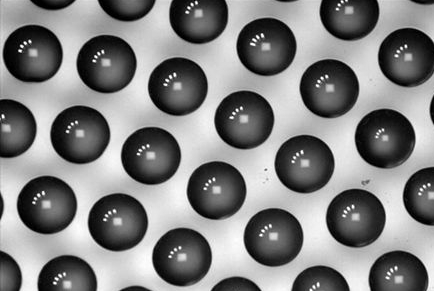
Laser swelling can be used for local swelling of partially transparent plastics without causing structural damage. Fraunhofer IMWS has been optimizing this technology for several years. In the "myLens" project, which was completed in March 2023 and funded by the Fraunhofer Future Foundation, the research team has significantly further the approach. For example, challenges relating to thermal management, dimensional accuracy, the influence of subsequent coatings, process control and the use of laser swelling on curved surfaces were successfully mastered. The result is a technology that can be used very universally and offers decisive advantages over the state of the art in many areas.
Microlenses produced using the patent-pending process are created by irradiating a plastic substrate with focused infrared laser radiation. This makes it possible to create non-contact and non-abrasive structures that are optically effective and can therefore be used for spectacle lenses, for example. One of the advantages of this is that the structures themselves can remain invisible - for example, they have no aesthetic impact when wearing glasses or allow products to be marked discreetly. Other areas of application could include intraocular lenses in AR/VR glasses, optics for LED displays, layer adhesion tests or use in microfluidics.
The high precision and reproducibility of the method allows numerous individual solutions. The solidification zones in the plastic substrate can be specified very precisely using the laser trajectory, allowing any shape of microlens (spherical, aspherical, etc.) to be produced. Their diameters can be set as required in a wide range from a few micrometers to millimeters and heights from a few tens of nanometers to a few tens of micrometers. The shape accuracy is in the nanometer range, the position accuracy in the micrometer range.
"The process is fully compatible with industrially used coating technologies for the functionalization of polymer optics. In contrast to molding processes, production can be carried out without tools and therefore without tool wear. For applications in the field of medical technology, individualization is thus possible for the first time, as the lenses are flexible in terms of geometry and arrangement," says Prof. Dr. Thomas Höche, Head of the "Optical Materials and Technologies" business unit at the Fraunhofer IMWS.
A prominent example of the benefits is the potential use of microlenses in the treatment of short-sighted children, a problem that is increasing worldwide. Short-sightedness (myopia) can lead to secondary diseases such as retinal detachment, macular degeneration or cataracts. Although conventional children's spectacle lenses correct vision, they do not stop the development of myopia. However, microlenses could help to prevent the progression of short-sightedness, as the growth in the length of the eye that causes short-sightedness can be slowed down or even stopped completely with the help of a superimposed focal point in the periphery. With laser swelling, appropriately structured lenses could be produced much more cheaply than with existing methods - and also individually tailored to the patient.