Inverters are crucial for modern energy systems. Despite the high level of quality that has been achieved for these complex components in recent years, device failures can also occur here. The causes of defects and failure processes are not yet sufficiently well understood. In the “Reliability Design” project, the Fraunhofer Institute for Microstructure of Materials and Systems IMWS has supported the development of more precise methods for lifetime predictions. This can also reduce the costs of electricity production.
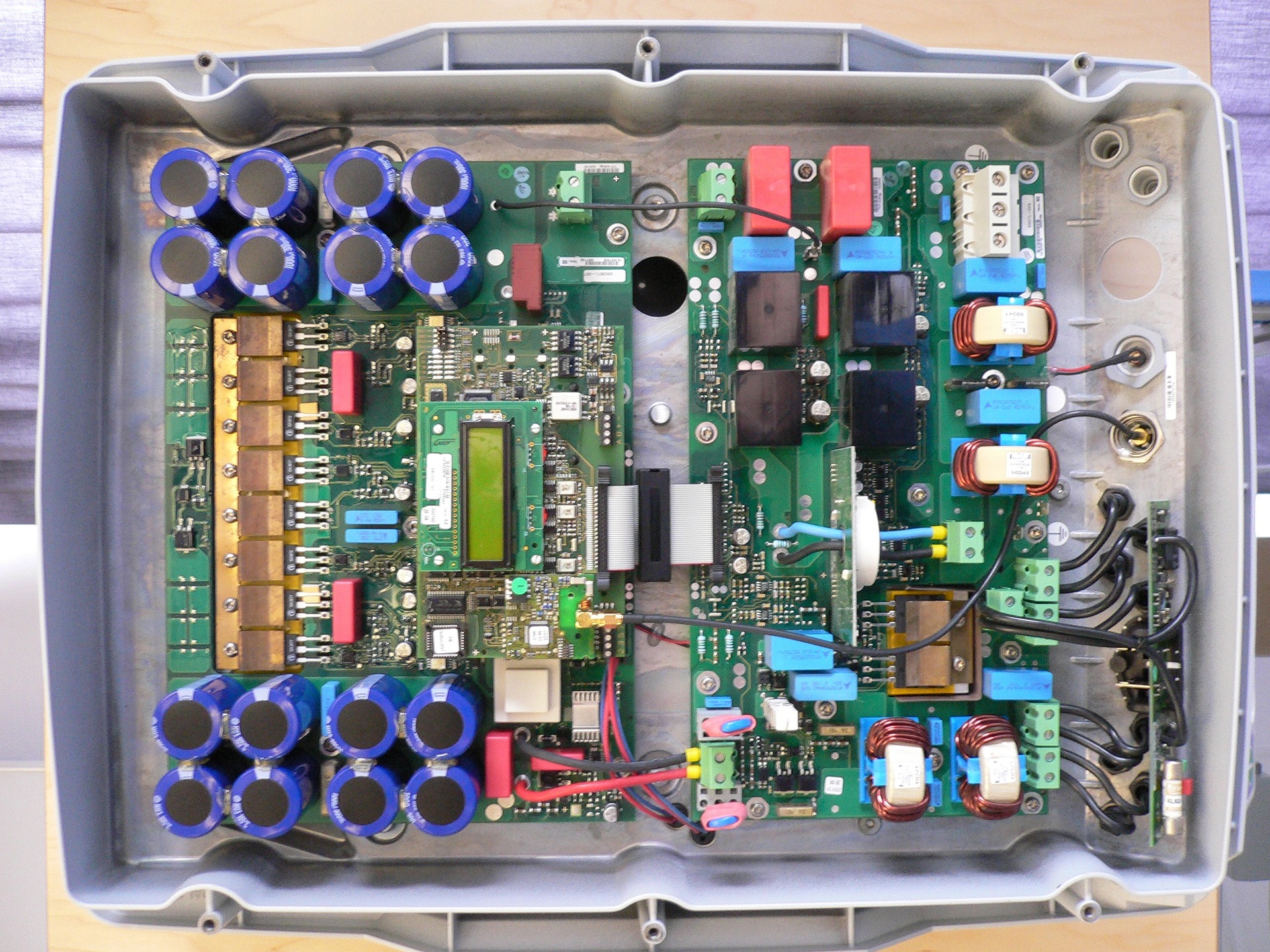
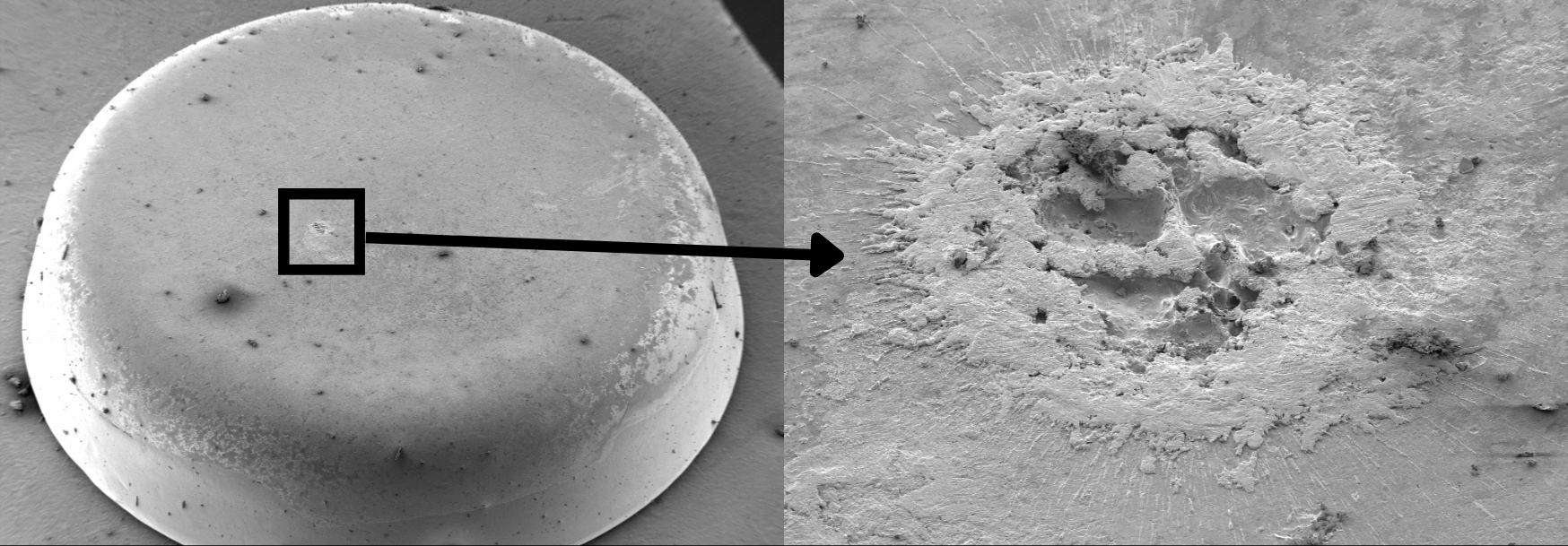
From household devices to power plants: inverters are used everywhere. Their importance has increased once again as a result of the energy transition, as they are also essential for photovoltaic (PV) systems, battery storage systems such as those used in electromobility and energy grid management. However, inverters in such systems are exposed to very challenging operating conditions: the effects of dirt, wind and weather, high voltages and almost non-stop operation. Their performance and quality are therefore of particular importance.
Despite these loads, high-quality inverters typically achieve a service life of 20 to 25 years. However, it is still largely unknown which construction methods, materials and designs ensure this, especially as there is still relatively little experience available for application scenarios such as photovoltaics or electromobility. For this reason, inverters are manufactured with safety margins and, in case of doubt, “oversized”: Manufacturers rely on production processes and materials with which the necessary robustness can be expected, but without an in-depth understanding of ageing processes, failure mechanisms or defect risks for the individual components within an inverter. This entails corresponding additional costs.
In the “Reliability Design” project, SMA Solar Technology AG (Niestetal), ELECTRONICON Kondensatoren GmbH (Gera), MERZ Schaltgeräte GmbH & Co. KG (Gaildorf), the Institute for Machine Elements at the University of Stuttgart and the Fraunhofer IMWS (Halle/Saale) have worked together to underpin and expand the existing empirical knowledge with scientifically sound data, models and measurement methods. The result is now an efficient and precise methodology for predicting the reliability and service life of PV and battery inverters and their critical components - and thus an even better basis for their reliable operation over their entire service life.
Precise design for the development of new inverters
“Our results enable a more precise design in the development of new inverters and faster tests during quality inspections. This reduces manufacturing costs because we have a much deeper understanding of the behavior of the components,” says Sandy Klengel, who led the project funded by the German Federal Ministry for Economic Affairs and Climate Protection (BMWK) at the Fraunhofer IMWS.
For “Reliability Design”, the institute in Halle (Saale) focused on clarifying previously not understood failure and ageing processes in film capacitors and electromechanical switching devices (DC disconnectors and relay assemblies), relying on in-depth physical and chemical analysis and modeling of the causes of defects and reliability risks. “In the consortium, we have specifically analyzed field data from inverter failures and also examined whether experience and methods from other application scenarios can be transferred to these phenomena. We can contribute an excellent understanding of material and component behavior in power electronics and extensive experience in the field of test development, analysis and evaluation of corrosion processes of microelectronic components,” says Sandy Klengel. “Thanks to the project, we have now also developed a great deal of expertise in the often particularly critical interaction of voltage, temperature and humidity on insulation materials.”
New methods for testing film capacitors and switches
A large number of defects and degradation mechanisms were deliberately provoked in the project under laboratory conditions, often using specially developed test setups, in which material interactions in the device, changing electrical loads or location factors such as seasonal temperature and humidity fluctuations or corrosive media such as salt spray were also taken into account. At the same time, an assessment was made as to which of these phenomena are actually relevant for use in the field and for reliable operation, for example by comparing them with components and parts that have aged free of defects in the field.
The findings concern, for example, cracks in ceramic layers, which can endanger the insulation strength of power modules, the formation of oxide layers, demetallization, polymer degradation, thermal damage due to overvoltage, solder degradation due to thermomechanical stress cycles, crystalline deposits, local melting, contamination with foreign material or the failure of housing components.
Failure catalog formulated for failure types, characteristics and causes
The results of the analyses on film capacitors were summarized in a failure catalog, which provides an overview of failure modes, failure characteristics, failure type and failure causes. In addition, numerical simulation approaches were used for an extended understanding of the physics of failure, for example to determine local current density and heat loss distributions in switches. “With the results, manufacturers can now reduce material requirements and testing costs and thus lower device costs - without compromising the reliability and service life of the inverters. This is also a contribution to making the renewable energy system more affordable,” says Klengel.
(October 22, 2024)