More than 100 guests discuss innovations at the third Composite Sandwich Conference in Halle (Saale)
The use of fiber-reinforced plastics in sandwich construction enables highly efficient lightweight structures. Leading international experts presented and discussed current trends in material and technology development and new fields of application for sandwich materials at the "Composite Sandwich Conference" on 24/25 April 2024 in Halle (Saale). They showed solutions in the field of tension between raw material efficiency, digitalization and sustainability, for example for applications in the automotive industry, aviation or photovoltaics.
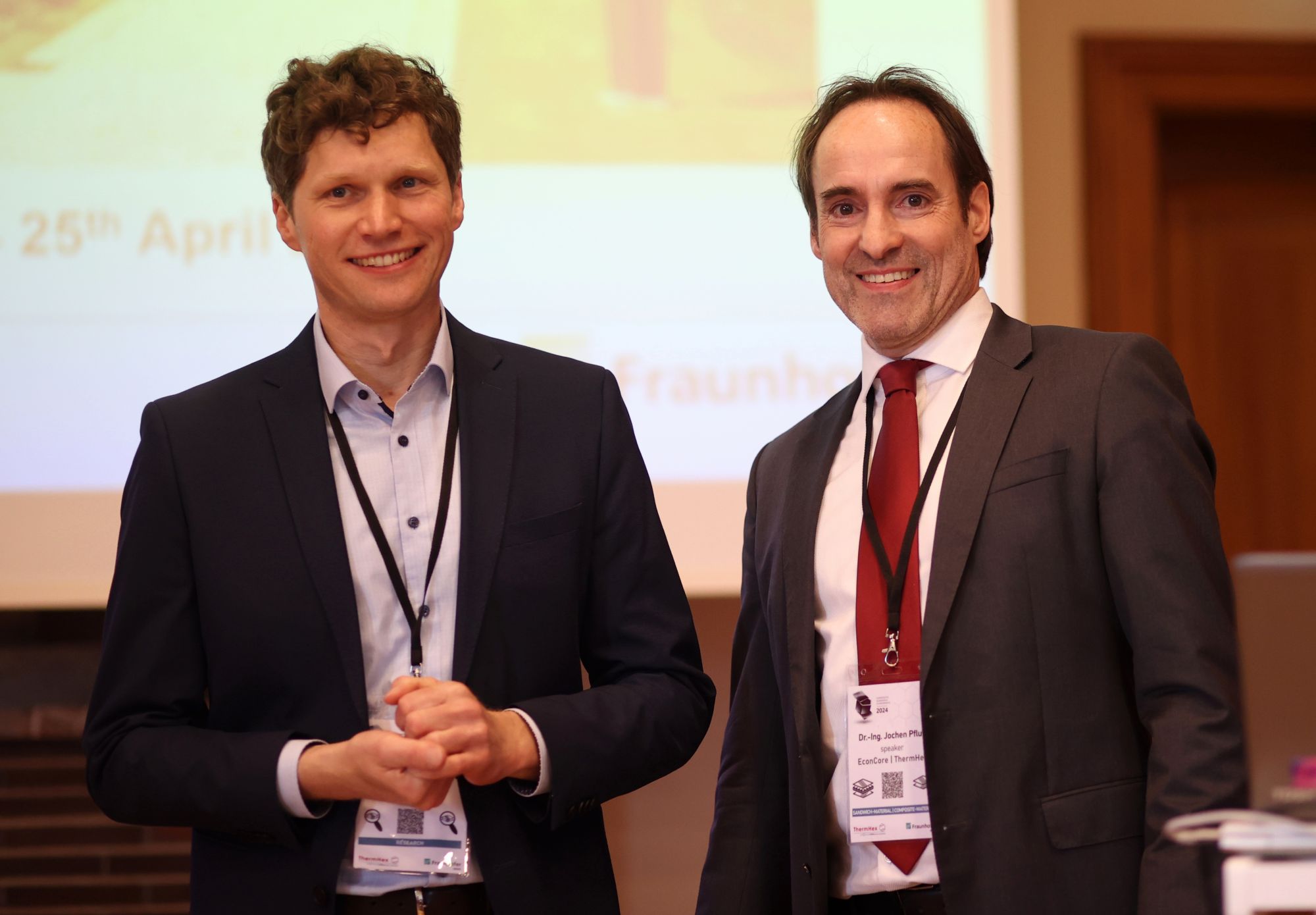
The conference was jointly organized for the third time by ThermHex Waben GmbH and the Fraunhofer Institute for Microstructure of Materials and Systems IMWS and attracted more than 100 international guests from industry and research to Halle (Saale).
Ignaas Verpoest, Professor Emeritus of the Composite Materials Group at the Catholic University of Leuven, opened the conference with his keynote speech "Innovations in composite sandwich structures: reflections on a personal journey". In his retrospective covering more than 30 years, he showed that in addition to creative inventors, a deep understanding of material properties, the further development of experimental methods and virtual models and, last but not least, a focus on the needs of industry are decisive criteria for successful material innovations.
The second day of the conference featured a variety of sessions on current R&D solutions for the consistent implementation of lightweight approaches with sandwich construction and sandwich core materials. Here it became particularly clear that these can score three times over in terms of sustainability: They often enable processes with significantly lower material usage in production than in monolithic construction. Thanks to their lightweight construction potential, they can contribute to reducing emissions during the use phase, for example by reducing the weight of vehicles. At the same time, thermoplastic mono-material sandwich components in particular offer considerable advantages in terms of recyclability at the end of their service life compared to thermoset fiber composite components.
"In the presentations and discussions with our guests, it became clear how important the balance between material performance and costs is. Many current developments and research projects are already addressing this ratio. I was also impressed by the wide range of applications and material solutions presented, from plastics to ceramics and wood," says Dr. Ralf Schlimper, who chaired the conference on behalf of the Fraunhofer IMWS.
"I am delighted that we were once again able to welcome such a high-caliber and large audience. The diversity of the industries that were represented underlines the enormous potential of sandwich construction for industrial applications," says Dr.-Ing. Jochen Pflug, Managing Director of ThermHex Waben GmbH and also organizer of the conference. During the conference, his company presented the new product "ThermHexWAVY" for the first time, a thermoplastic honeycomb core with a wave-shaped cell wall geometry that enables significant increases in compressive strength. The special geometry can be produced with any thermoplastic polymer on the existing ThermHex production lines.
Other innovations presented at the Composite Sandwich Conference included applications of sandwich technologies in helicopter structural components (Airbus Helicopters), as protective structures in the underbody of electric vehicles (Audi AG) and as an aerodynamic underbody for sports cars (Porsche). Recyclable thermoplastic core materials which are particularly flame-retardant for interior components in aircraft were another focus. Evonik Operations presented a foam core material made of polyetherimides (PEI) based on pre-foamed micro-granules and ThermHex presented a PEI honeycomb core. Solarge demonstrated the potential of sandwich construction for photovoltaic applications, such as particularly lightweight modules that can also be installed on roofs with insufficient load-bearing capacity for standard modules.
"The content of the sessions showed how dynamic the development is and how high the level of activity in the industry is in order to save not only component weight but also material," said Pflug at the end of the conference, which also included a company and product exhibition as well as visits to the ThermHex production facility and the Fraunhofer sites in Schkopau and Halle. "The presentations also highlighted the need for further research, from in-depth findings on material properties and material development to solutions for quality and process control and efficient ways to reduce the amount of material used for thermoplastics in structural applications to the development of methods for specific designs," concludes Schlimper.
The next Composite Sandwich Conference is planned for spring 2026.